Safety Risks in CNC Bending Machine Operation and Safety Light Curtain Solutions
Safety Risks in CNC Bending Machine Operation and Safety Light Curtain Solutions
CNC bending machines are indispensable equipment in modern sheet metal processing, widely used in industries such as automotive, aerospace, light industry, shipbuilding, containers, elevators, and railway vehicles. During the efficient bending process, operators face various potential safety risks, including mechanical pinch hazards, operational errors, and machine failures. Therefore, ensuring operator safety and preventing equipment malfunctions and human errors have become key tasks in the CNC bending machine work environment.
To enhance the safety of CNC bending machines, safety light curtains, as an effective safety protection measure, play an important role in preventing accidents. Below, we will explore the safety risks associated with CNC bending machine operations and how safety light curtains can reduce these risks.
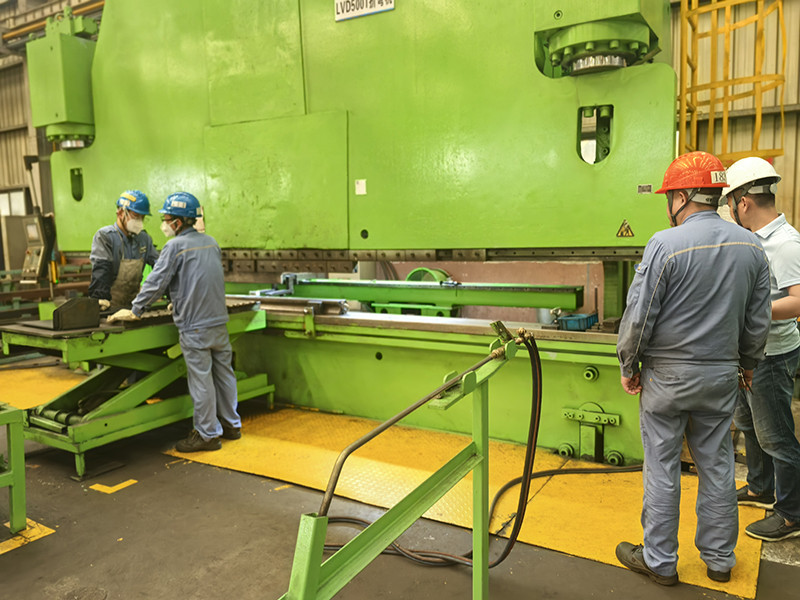
Common Safety Risks in CNC Bending Machine Operation
In CNC bending machine operations, the main safety risks include mechanical pinch hazards, operational errors, equipment failure, and unexpected startups or reverse operations. These risks can lead to injury to operators or damage to the equipment, especially when the slider is in motion, making it easy for hands or body parts to be pinched. Furthermore, improper operations or equipment malfunctions may result in accidents. Therefore, implementing safety protection measures such as safety light curtains can effectively reduce these risks and ensure the safety of operators.
Safety Light Curtain Solution
Safety light curtains improve the safety of CNC bending machines through real-time monitoring and protection, fast response, non-contact protection, and adaptability to various working environments and operating modes. They can detect if an operator enters a hazardous area and quickly trigger an emergency stop to prevent incidents such as pinching. Additionally, safety light curtains require no physical contact, reducing the likelihood of faults, and they can operate stably in various environmental conditions. This not only reduces equipment downtime but also ensures that operators are protected in any operational state, greatly enhancing both production efficiency and safety.
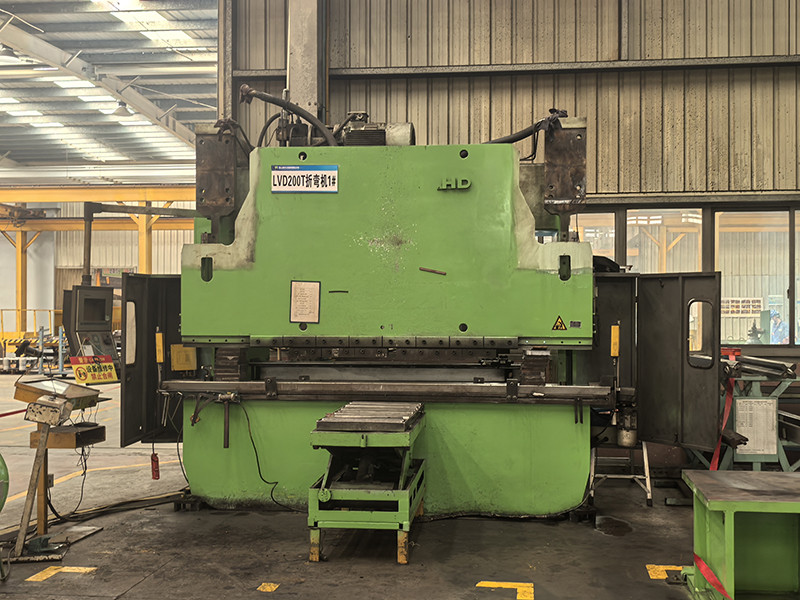
Considerations for Implementing Safety Light Curtains
When implementing a safety light curtain solution, the following points should be noted:
▪️ Selection and Installation Position: Choose the appropriate safety light curtain model based on the specific working environment and operational requirements of the CNC bending machine. Ensure it is installed in areas that effectively protect operators. The light curtain should cover potential hazardous areas, such as the path of the slider and places where operators might approach.
▪️ Regular Inspection and Maintenance: The effectiveness of safety light curtains depends on their stable operation, so regular inspections and maintenance are necessary to ensure sensor sensitivity and accuracy. This prevents any malfunction that could compromise the protection system.
▪️ Operator Training: In addition to installing safety light curtains, it is crucial to provide proper safety operation training for operators. They should be familiar with the machine's operating procedures and know how to handle emergency situations.
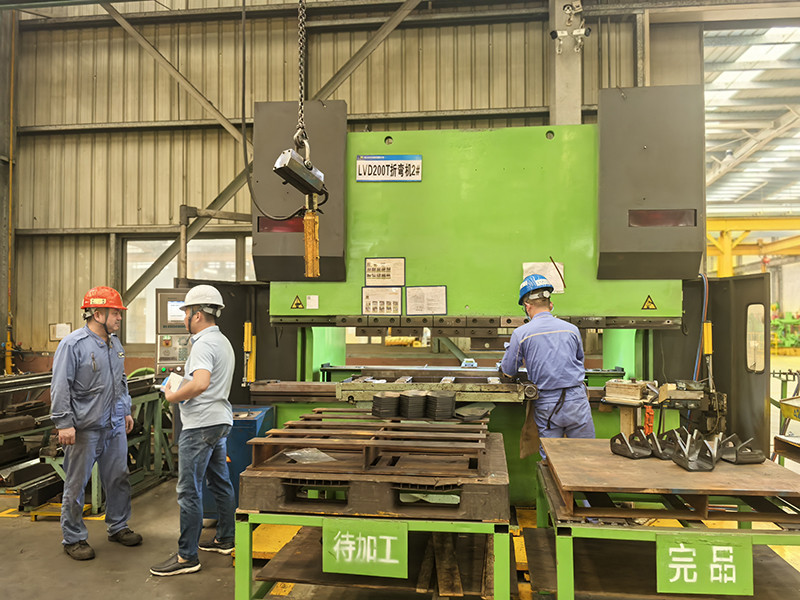
Related Safety Light Curtains
DADISICK is a professional manufacturer of safety sensors with solid product manufacturing capabilities.
DADISICK is a professional manufacturer of safety sensors with solid product manufacturing capabilities.
DADISICK is a professional manufacturer of safety sensors with solid product manufacturing capabilities.
DADISICK is a professional manufacturer of safety sensors with solid product manufacturing capabilities.