Efficient Application Solution of Ultrasonic Sensors in Cement Silo Level Monitoring
Efficient Application Solution of Ultrasonic Sensors in Cement Silo Level Monitoring
Background
In modern cement production, precise monitoring of silo levels is critical to ensuring continuous production and improving product delivery efficiency. However, traditional monitoring technologies often face issues such as dust accumulation and environmental interference, which compromise measurement accuracy, leading to delayed replenishment or even production interruptions.
To address these issues, the CSB30 ultrasonic sensor provides a reliable, cost-effective, and efficient technical solution for cement silo level monitoring, with its non-contact detection, high measurement accuracy, and outstanding environmental adaptability.
System Components

1. Core Component: CSB30 Ultrasonic Sensor
▪️Function: High-precision level monitoring with vibration-level switch functionality.
▪️Features: No moving mechanical parts, resistant to dust accumulation, and supports long-term stable operation.
2. Signal Transmission Line
▪️Uses high-quality shielded cables to effectively reduce electromagnetic interference, ensuring accurate and stable signal transmission.
3. Data Processing Unit
▪️Equipped with industrial computers or intelligent instruments for receiving and processing sensor data, supporting data display, historical storage, and alarm settings.
4. Alarm Device
▪️Includes audible and visual alarm modules that provide clear signals to notify staff of any abnormal levels, preventing incidents.
Ultrasonic Technology
1. Ultrasonic Emission and Reception
The CSB30 sensor emits ultrasonic pulses towards the surface of the cement in the silo. These pulses are reflected back to the sensor upon reaching the cement surface.
2. Level Calculation
By calculating the time difference between the emission and reception of the ultrasonic pulses and considering the speed of sound in air, the sensor determines the distance between itself and the cement surface. The height of the material level in the silo can then be calculated, and the actual cement quantity can be derived by combining the silo’s geometric parameters.
3. Status Assessment and Alerts
The data processing unit analyzes the sensor data to determine whether the silo is in a full, empty, or normal state and sends corresponding signals to the alarm device.
Your Advantages At a Glance
High-Precision Detection
The CSB30 ultrasonic sensor series reliably and accurately performs level detection tasks, providing precise data support for cement silo level monitoring.
Easy Installation and Debugging
The sensor is easy to install and does not require silo filling for debugging, significantly reducing installation and commissioning time and costs.
Stable and Reliable
The design without moving mechanical parts prevents wear and tear, while its resistance to sediment accumulation allows for long-term stable operation in harsh working environments.
Real-Time Monitoring and Alerts
With the data processing unit and alarm device, real-time monitoring and early warnings of cement silo levels are achieved, enabling timely identification and resolution of potential issues to ensure smooth production.
Implementation and Maintenance
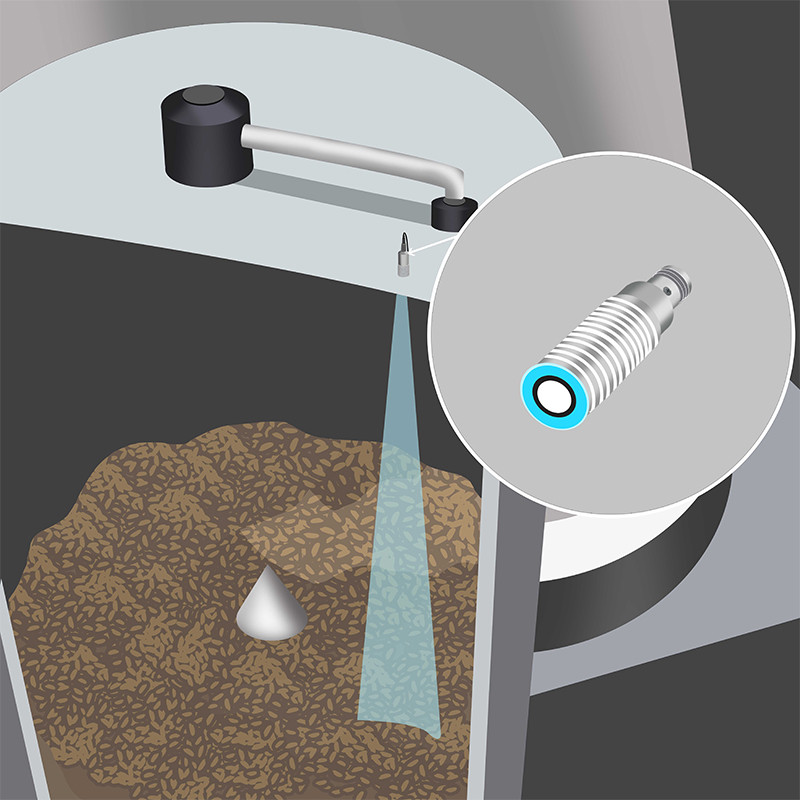
Installation
Install the CSB30 ultrasonic sensor on the top of the silo, ensuring the emission direction is perpendicular to the cement surface.
Connect the data processing unit and alarm device using professional wiring methods to complete system setup.
Calibration and Debugging
Perform initial calibration after installation to ensure measurement accuracy.
Set alarm thresholds based on production requirements, such as issuing a refill warning when the level is below 20% or a stop-filling alert when it exceeds 95%.
Routine Maintenance
Regularly clean the sensor surface to prevent dust from affecting signal transmission.
Check the connection status of signal cables and data processing equipment to address potential issues promptly.
Conduct comprehensive calibration and performance testing every six months to ensure long-term reliability of level monitoring.